Home » Heating and Cooling - Install » Page 43
Page 43«..1020..42434445..5060..»
James Nani Times Herald-Record @JamesNani845
MIDDLETOWN - A large-scale replacement of city residents' water meters is expected to begin in the next few weeks, part of a $12.7 million conservation project approved last year.
The first of nearly 8,000 state-of-the-art Sensus water meters arrived last week at the city's former water-treatment plant near Monhagen Lake.
Subcontractor Professional Meters Inc. isstaging its operation there as it gets ready to canvas the city and install the meters in homes and businesses, according to Jacob Tawil, commissioner of the city's Department of Public Works.
The new meters will be attached to radio transmitters and will beam hourly radio signals providing information to the city about water usage.
About 7,500 homes and 400 businesses will get new meters, Tawil said. Letters will go out to recipients in the next few weeks.
Older meters will be collected and stored for about a year in case residents lodge complaints about the new ones.
The installations are expected to take from April to October.
Tawil said the new meters will be more accurate, will allow people to see exactly how much water they're using and will save on manpower because city workers won't need to drive by homes and businesses to pick up radio signals.
But Tawil said the biggest reason for the change is to save water.
"I've been trying to do this forten of my lasttwelve years here, since I've been at City Hall," Tawil said.
According to the Sensus website, the meters are able to capture low-flow water that other meters cannot- flow rates as low as 0.1 to 0.3 gallons per minute.
The meters will also allow users to check online and monitor leaks and drips to help save water.
The installation, which Tawil said is expected to cost about $5 million, is part of a $12.7 million package of energy- and water-conservation projects for which the city has hired Energy Systems Group (ESG), based in Tennessee.
Middletown is using bonds to pay for the work.
The upgrades are ongoing. The city is preparing to install solar panels next to the water-treatment plant to reduce the plant's energy costs.
Old boilers and heating and cooling systems in several city buildings have been replaced.
And last week on West Main Street, subcontractors climbed up ladders to replace incandescent bulbs with LED lights.
In total, the changes are supposed to save the city $18.6 million over 15 years, according to the contract.
If the energy savings aren't met, the contract says ESG will cut a check for the difference.
The project is supposed to be completed within 12 to 18 months.
jnani@th-record.com
Read the rest here:
Middletown to install new high-tech water meters - Times Herald-Record
Advanced technology has brought a lot of convenience to people, from smartphones to smart appliances. Home automation systems have been a huge hit especially with people who want to have easy access and control to their appliances. Automation systems are controlled through smart gadgets and can be installed with 12v actuators in order to obtain comfort and elegance. That is why selecting the best linear actuator is also important. Linear actuators are becoming more popular for automation and smartification. Actuators allow for a free range of motion depending on an application that an engineer or a home builder alike. The system can control the lighting, heating, ventilation, and even security locks inside the house. The appliances should be compatible with each other and are all connected to a centralized control unit. To even make things easier, mobile gadgets such as iPad, iPhone, tablets, and android phones can be used to control the smart appliances.
Using home automation systems gives a comfortable, convenient and safe lifestyle to families. By simply tapping your phone, you will be able to monitor everything that is happening around your house through the smart security gadgets like video cameras, smart locks, and smart doors. The use of automation systems increases energy efficiency while reducing the heating and cooling costs.
Making a Home Automation System with android is something that requires a lot of skill, patience, and resources. The project aims to allow the users control appliances wirelessly by integrating a specific system to the buildings electrical system.
Any mobile device with Bluetooth or WiFi can be used to control the system. The server will be a microcontroller powered box. There will be minimum costs for the installation and hardware since users already own mobile gadgets.
If you are planning a DIY smart home automation project, there are a couple of things that you have to know first. You must be knowledgeable with some basic carpentry, programming, and some basic electronics. Starting a DIY home automation project will also require some hardware which requires some technical materials. You can easily search the internet for electronic circuit board designs to design the set-up of your home system. Here are the things that you need to create and arrange so that you can finally have the home you deserve.
A block diagram is a simple visual aid that shows the basic components of the home system that you are creating. It shows the centrality of control, the presence, and features of the home automation system and the major electronic components and devices that will be installed. Here is the block diagram of a home automation system.
The Circuit diagram is a more complex diagram which will show the circuitry of all the electronic components that has to be set-up. To make a circuit diagram, you need technical knowledge with electronic components and how to handle and put them together. If you are in doubt with your Circuitry skills, you can simply try and learn from the internet.
A PCB or a plastic circuit board is a specially designed electronic diagram. It physically connects the different parts and components of the system. You might need the skills for arranging and soldering parts together. The circuit board must be made precisely to prevent short circuiting.
The automation system is managed with small computers. One brand is the Arduino, which is popular due to its easy interface and coding flexibility. Many home automation enthusiast choose Arduino as it is compatible to any appliance and can easily be programmed with Android devices. Androids software is easily one of the most popular since it uses complex codes that can be programmed with anything.
The final element that is needed in a home automation project is, of course, the Android App. This Application offers the centrality of control of your home automation system. The applications interface depends on the appliances, sensors, and actuators that you install with your home automation system. The app can regulate temperature, automatically switch lights on and off, analyze the users preferences and track sleep patterns.
Making a DIY Home Automation system is hard work but it is also worth it. The process can be enlightening in many ways but most importantly, you are bringing comfort, elegance, and ambiance to your house. You are turning the physical spaces and materials of your house into a cozy home.
Read more:
DIY Smart Home Automation Using Android - TG Daily (blog)
COUPEVILLE Private air-jet massage tubs for mothers-to-be. Skylights shining above waiting rooms. Patient rooms larger than apodments in Seattle and tiled bathrooms nicer than most motels.
Shades of the colors Quietude, Humble Gold and Nomadic Desert.
Those are among the more obvious differences between the old and new of WhidbeyHealth Medical Center, set to open its $33.3 million-plus addition this year. That amount doesnt include taxes, legal fees, architects, permitting, water, sewer, power, engineering, said Patricia Duff, a WhidbeyHealth spokeswoman.
The two-story, 60,000-square-foot expansion will replace the current intensive care unit, medical and surgical patient rooms and labor and delivery suites.
All 39 rooms are single patient rather than shared. This trend in hospital design the past decade has shown to reduce infection rates and increase patient privacy and rest.
Theres also many more subtle state-of-the-art features of the renovation that are part of the upgrade.
An innovative heating and cooling system developed in Japan is expected to substantially lower energy bills.
And a myriad of infection control features, including smooth, non-porous and easily cleanable walls and floors, increased hands-free sinks and more airborne infection isolation rooms should mean a safer hospital.
Preventing transmission of infectious agents to vulnerable patient populations, health care personnel and visitors is a priority at WhidbeyHealth, said nurse Colleen Klamm, the hospitals infection preventionist.
The $50 million project bond, approved by voters in 2013, costs property owners an estimated 32.2 cents per $1,000 assessed property value over 25 years.
Patients can expect a more healing environment when the medical centers new wing opens in late spring, said WhidbeyHealth CEO Geri Forbes.
We have always provided great care, she said. Now we will have an environment that is as good as our doctors and nurses.
Attention to detail is based on the experience of other recently-constructed hospitals around the country and extensive studies of inpatient care, Forbes said.
In the past 50 years, inpatient care has made enormous strides in treatments, quality, technology, equipment, infection control, safety and privacy, she said. The new wing will reflect these advances while eliminating the complexity of double patient rooms.
Construction is about 74 percent complete, said George Senerth, executive director of facilities for the health care system.
Interior work began in December.
Andersen Construction is the main contractor. HDR Architecture and Engineering Firm, a global company with 50 years experience planning health care facilities, designed the addition.
In addition to paying for the new wing, the bond also provides for remodeling of existing patient rooms into pre- and post-operative areas, a new loading dock, an expanded parking lot and a new exit area to discharge patients.
Whidbey General was built in 1970 and voters approved three expansions over the past 46 years, said Keith Mack, community relations manager for WhidbeyHealth.
Some 20,000-square-feet of the additions first floor will remain undeveloped and available for future use, said project manager Mark Estvold.
The new wing is divided into east and west pods separated by a corridor, reception desk and waiting areas. The central corridor will house nutrition, medication and other supplies.
Every room will be a mirror image, with beds, cabinets and supplies all located in the same places, said Annette Himelick of HDR Architecture.
Theres nothing more disconcerting than a doctor coming into a room and looking around wondering where the gloves are, she said. Standardizing the room is done through design.
The new one-patient medical/surgical rooms measure 280 square feet. Thats bigger than the current patient rooms that hold two beds and measure 160 square feet.
Labor and delivery suites will also be noticeably roomier at 392 square feet with bathrooms measuring 87 square feet.
Large white soaking tubs in the birthing suites bathrooms are not standard hot tubs and they arent used during delivery, Klamm said.
The tubs work like a geyser shooting out streams of heated air so water is constantly circulating, providing a gentle therapeutic massage that may help induce labor.
Last year, 181 babies were born at WhidbeyHealth Medical Center.
Additionally, almost every room has a motorized lift above the bed.
This not only helps handicapped patients but saves the backs of staff, said nursing manager Patsy Kolesar-Hynson.
Huge, huge, is how she describes the impact the new wing will have on patients and her 80-person staff.
The rooms we have now look great when you dont have any patients, she said, but add the patient, equipment, family, it gets very cramped, very quickly.
Nurses can also expect to spend more time with patients because of a design change. Instead of a large centralized desk where they typically gather and record information, theyll work from small work stations in the hallways directly outside patient doors.
Mary Bridge Childrens Hospital in Tacoma studied time its nursing staff walked up and down hallways getting to patients versus time spent with patients before and after a similar upgrade, Himelick said.
Nurses spent only 31 percent of their time with patients before the renovation. After setting up small stations outside every other room, time with patients increased to 75 percent, she said.
A nurse server pass-through slot on patient doors is another design change. Accessible from the inside and outside, supplies, linens and trash can be slid through the slot, meaning more peace and quiet for patients because staff wont be in and out so often.
We want to minimize the disturbance to patients as much as possible, Himelick said.
And we dont need nurses walking six to 10 miles a day.
Coffman Engineers, a consultant to HDR Architecture, is leading the installation of an innovative heating and cooling system known as a variable refrigerant flow heat pump system. It transfers heat from an unoccupied room to a room in use, potentially reducing energy use by 40 percent.
Students with the University of Washingtons Integrated Design Lab are tracking the project to gauge energy savings.
More here:
$50 million hospital expansion set to open later this year - The Daily Herald
| Firefighters concerned about conditions at Bragg stationNews & ObserverFirefighters at a fire station on the Fort Bragg have turned to Congress for help with repairs at a fire station that has a leaky roof, holes in the walls, mold, asbestos and even a fire alarm system that's not in compliance. The Fayetteville Observer ...and more » |
See the original post here:
Firefighters concerned about conditions at Bragg station - News & Observer
'); //-->
PHILADELPHIA The Indian River Central School District is embracing clean energy with its planned installation of a geothermal heating system.
District Business Administrator Joseph A. Dougherty said he anticipates that the oil tanks will be removed from the high school as soon as they are shut off.
Weve actually had geothermal power at the intermediate school since it was constructed in 2002, Mr. Dougherty said.
The Indian River Intermediate School is also home to the districts solar panel array, with its construction being completed in Oct. 2016.
Mr. Dougherty said the district anticipates that the funds originally intended for fuel oil, $250,000 according to current budget documents, will cover any increased electricity costs.
Geothermal power involves heating and cooling water underground and then using that water to either heat or cool the air. The steam is also sometimes used to power electricity.
Noah A. Prior Jr., Facilities Director at Indian River, said that the high school is already partially powered by geothermal energy and the final 140 wells have been installed nearly 500 feet into the ground.
The last step now is to install the pipes and remove the conventional heating system. Youre dealing with equipment thats probably 30 or 40 years old, he said.
In order to make sure the high schools final push to green energy is the right choice, the facilities department first reported its energy costs at the intermediate school to the New York State Energy Research and Development Authority.
We sent them our bills for about a year and they determined that our geothermal system there was 99 percent more efficient than a conventional one, Mr. Prior said.
The improvements at the Indian River High School are part of a Capital Project in partnership with NYSERDA.
Other buildings within the district use geothermal power: Theresa Primary School installed their systems in 2002, and Calcium Primary has gotten half its power from geothermals since 2010.
The district hopes to continue its environmental stewardship by using renewable energies in its other buildings.
Were excited about this move to green energy, Mr. Dougherty said, This has been a Board of Education priority for at least five years.
Read more from the original source:
Indian River High School plans to switch to geothermal power - WatertownDailyTimes.com
Today, we will set an example for the world: with boldness, with confidence and relentless optimism. In accordance with the companys guidelines, the Indian car manufacturer, Mahindra & Mahindra Limited, is maintaining its sustainable strategy for production facilities. This is the reason Mahindra has contracted the German plant manufacturer, Durr, to install an innovative and environmentally-friendly painting line in Pune, India. After the first year of production the rsum now is: the expectations have been met. The new line includes the first time installation of Durrs EcoDry X cardboard filter box system which ensures cost and energy efficient overspray separation.
Following the start of production in November 2015, the plant was ramped up to its maximum annual capacity of 91,000 units. The scope of supply consisted of a painting line including spray booth, air handling equipment, oven and conveyor. In order to meet Mahindras goals of simplicity, reduction of resources and energy consumption, as well as the reduction of the companys water footprint and paint sludge, Mahindra set a new standard for the top coat line. This was done by choosing the latest Drr Eco+Paintshop products such as Eco+Layout, EcoSmart AC and EcoDry X.
With the Eco+Layout it was possible to create a simplified and more compact building design by placing the spray booth air recirculation unit which is operator-friendly on the ground floor. The add-on of the EcoSmart AC to the regular air conditioning control system in the spray booth air handling units optimizes energy consumption during production, especially in start-up times and extreme weather conditions. The improved control of the process window leads to major energy savings in cooling and heating, including a reduction of CO2 emissions.
With the selection of the cardboard filter box system EcoDry X from the Drr dry separation family, Mahindra avoids all coagulation chemicals and water in overspray separation and resulting paint sludge. EcoDry X is a semi-automatic filter system consisting of a filter trolley equipped with six filter boxes. The disposable cardboard filter boxes can be swiftly replaced with minimum effort using the filter trolleys even during production, if necessary. The system is simple and robust and can be easily operated.
With more than one year in operation, the performance of the cardboard filter boxes during their first application has exceeded customer expectations when it comes to handling and filter box consumption. The filter boxes of the EcoDry X set a benchmark in paint separation capacity and filter costs. This efficiency is based on the principle of the technology: No impact separation, but filtering is the order of the day. Further highlights are the EcoClean and the top coat heat exchanger. EcoClean is a feather duster unit at the start of the top coat line for the improvement of the exterior surface cleaning quality. The installed air-to-air heat exchanger at the exhaust duct of the top coat oven preheats, depending demand, the recirculated air to the air supply unit.
As provision for future sustainable technology, Mahindra designed the roof of the building for the installation of a solar-thermal oven pre-heating system. This will help the customer to reduce the heating energy and CO2 emission even further.
Due to the good and energy optimized performance of the new TC-Line, Mahindra has contracted Drr to increase the capacity of the line to up to 120,000 units per year.
The Drr Group is one of the worlds leading mechanical and plant engineering firms with outstanding automation expertise. Products, systems and services offered by the Group enable highly efficient manufacturing processes in different industries. Drr supplies not only the automotive industry but also other sectors such as the mechanical engineering, chemical and pharmaceutical industries, and since the takeover of HOMAG Group AG in October 2014 the woodworking industry. Drr has 92 business locations in 28 countries. With 15,200 employees, the Group generated sales revenues of 3.57 billion in 2016. The Group operates in the market via five divisions:
Visit link:
First time installation of Durr's EcoDry X technology worldwide - Automotive World (press release)
Category
Heating and Cooling - Install | Comments Off on First time installation of Durr’s EcoDry X technology worldwide – Automotive World (press release)
| Top 150 2017: No. 44 Marcone SupplySt. Louis Business JournalThe company sells parts for property maintenance, cooling and heating, installation and appliances. Featured vendors for the firm include KitchenAid, Whirlpool and Maytag. In addition, Marcone exports parts to clients in 120 countries around the globe. |
See more here:
Top 150 2017: No. 44 Marcone Supply - St. Louis Business Journal
Heavy equipment and fencing is now on full display on the PCM Middle School/Prairie City Elementary campus, as a nearly year-long construction project began Tuesday on the exterior of the two buildings.
Crews began removing trees, brush, shrubs and concrete to clear the path for primary construction, slated to start after students leave for summer break in May. The work is all part of PCMs three-year, $20 million facilities renovation project.
At Monday nights monthly school board meeting in Monroe, PCM Superintendent Brad Jermeland updated board members on construction progress, including interior renovations to PCM Middle Schools auditorium, which began during last weeks spring break.
Asbestos removal from the auditorium and gym was completed Thursday. Construction crews have removed the existing seats and carpet in the auditorium to prep for expanding seating, making stage improvements and other upgrades.
But the most noticeable changes are outside the school, where the former parking lot and bus lane between the schools has been fenced in and transformed into a work zone. By the end of next school year, the area will hold an enclosed breezeway linking the two buildings.
The districts new pick-up and drop-off policy for students and parents was implemented Monday, and PCE Principal Stephanie Ver Helst said it went off without a hitch.
American Fence Company came out and put the fencing up on the property to define different zones for construction. I think that really helped out (Monday). It gave a clear picture of where people could travel and not travel, Jermeland said.
As trees were marked for removal, district officials found at least one was donated and dedicated by a Prairie City family. Jermeland said hes reaching out to any family or individual who donated a tree and will extend the opportunity to replant the variety of their choosing after construction is complete.
This is just the beginning of site work, which Jermeland said will consist of establishing staging areas for the construction companies, tree/bush removal, sidewalk/parking lot removal and dirt work for the Link addition that will be built to connect the two buildings.
The district announced its construction timeline for its Prairie City campus earlier this month.
Late site work in Prairie City will consist of final site grading and installation of new sidewalks to the entrances and adjacent areas. The middle school/PCE parking lot will be completed summer 2018.
Interior construction at PCM Middle School will last through September 2017. Work for the building addition is expected to start in early May and last throughout the 2017-18 school year.
The middle school media center will be renovated this summer, scheduled to begin at the end of May with a tentative finish date in the end of August. The current office area will be renovated this summer into classroom space and will be completed by fall.
Monroe Elementary
Project contractors also began putting the finishing touches on Monroe Elementary School during spring break. Two large cranes were brought to the facility last week to install the rooftop condensers and heating/cooling units.
Read more:
Under Construction - Newton Daily News
Allegheny Restoration and Builders Incorporated out of Morgantown are replacing and restoring some of the windows in the A.F. Kisar House on Third Street.
Main Street Point Pleasant has helped secure the funds for the continued restoration of the historic Kisar home.
POINT PLEASANT Restoration efforts are continuing on a historic home in Point Pleasant.
Several windows in the A.F. Kisar House, located on Third Street, are being replaced/restored to their original appearance, thanks to two grants one from the West Virginia Division of Culture and History and a Governors Community Participation Program Grant. Matching funds were also provided from Main Street Point Pleasant.
The grant applications had been completed some time ago, and work has been planned for the last couple of years. Though progress is sometimes slow, regardless of the pace, forward motion is still progress. In all, the work on this portion of the windows will cost around $75,000, total, Main Street Point Pleasant Treasurer Darlene Haer said. Allegheny Restoration and Builders Incorporated out of Morgantown is doing the unique work and will likely be done by the end of this month.
Main Street Point Pleasant has gone after all the funds to restore the home in the last several years with that restoration including: $200,000 for the roof and gutters; $546,000 for exterior brick and mortar wok, restoration of the front and side porches and installation of a handicapped ramp. The organization has raised around $821,000 so far for restoration efforts. Main Street Point Pleasant Executive Director Charles Humphreys said the next step will be looking for grants to install a heating and cooling system to maintain the temperature in the home which he hopes will eventually serve as a museum in some capacity.
Humphreys has long said the home is a showplace and theres no other quite like it in the state of West Virginia.
We are West Virginias best kept secret, Haer said about the tourism sites in Point Pleasant.
Main Street Point Pleasant has actually had a hand in developing some of those tourism sites, like Riverfront Park and its murals. The organization is also the longest running Main Street program in the state. In addition to Haer, Board Members include Sandy Dunn, Judy Hensley, Elizabeth Jones, Georgianna Tillis, Paul Simon, Joe Supple, Ed Lowe, Ruth Finley, Brian Billings, Bob Doeffinger, Denny Bellamy, Sharon Stapleton. The late Carolyn Harris was also a well-known member of the board.
With Gov. Jim Justice running on a platform of promoting tourism in West Virginia when he was a candidate, Humphreys is hoping Point Pleasant benefits from this in some way down the road, though but he and Haer are aware of the budget situation the state is in at the moment. Funds are drying up for projects like the Kisar Home.
Haer said if anyone has any ideas in terms of going after funding, or fundraisers, they should contact herself or Humphreys. Main Street Point Pleasant can be reached at 304-675-3844.
Allegheny Restoration and Builders Incorporated out of Morgantown are replacing and restoring some of the windows in the A.F. Kisar House on Third Street.
http://mydailyregister.com/wp-content/uploads/2017/03/web1_3.23-PPR-Kisar-1.jpgAllegheny Restoration and Builders Incorporated out of Morgantown are replacing and restoring some of the windows in the A.F. Kisar House on Third Street.
Main Street Point Pleasant has helped secure the funds for the continued restoration of the historic Kisar home.
http://mydailyregister.com/wp-content/uploads/2017/03/web1_3.23-PPR-Kisar-2.jpgMain Street Point Pleasant has helped secure the funds for the continued restoration of the historic Kisar home.
Window replacement ongoing at Kisar house
Reach Beth Sergent at [emailprotected] or on Twitter @BSergentWrites.
.
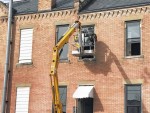
See the rest here:
Restoration efforts continue on historic home - Point Pleasant Register
Replacement windows can be a smart investment in comfort and design appeal of a home.
Replacing old windows is often a worthwhile investment for homeowners. Energy-efficient windows can prevent heating and cooling loss and keep homes more comfortable throughout the year. Such windows also can improve a homes resale value, proving a good return on investment for homeowners who want to upgrade their homes before putting them on the market.
According to the U.S. Department of Energy, homeowners might find it more cost-effective to replace very old and/or inefficient windows to improve their energy efficiency. Such an upgrade can save homeowners substantial amounts of money on heating and cooling costs.
Window replacement projects can be costly, so it pays to get the job right the first time. Before beginning a window replacement project, homeowners should research which windows will meet their specific needs, learning the subtleties between finishes and features, as well as comparing prices for the windows and installation.
The best time of year to plan window replacement is when the weather will be warm, ideally in the spring or early summer. However, homeowners do not want conditions to be too warm, as each room where new windows will be installed will temporarily be exposed to the elements. Furthermore, caulk adheres better in warmer weather and will dispense easily.
When replacing windows, homeowners may want to install the same style windows they currently have. But the problems that led to the need to replace windows may still exist even when new windows are installed. When replacing windows, consider energy performance ratings based on the locations of the windows in the house. To make sure they make the most educated decision, homeowners can investigate the solar heat gain coefficient, U-factor, visible transmittance and light-to-solar gain. Explanations of these ratings are available at Energy.gov.
Maintenance costs involved with cleaning, repairs and painting can add up. When shopping for windows, consider the amount of maintenance they will need. Wood-framed windows may require more upkeep than aluminum, fiberglass or vinyl. Also, consider if certain window types, such as double-hung windows, casement windows, awning windows, or slider windows, would be practical.
A poor match between windows and the style of the home can produce unwanted changes in the appearance of the home. Replacement windows should match the style and appearance desired.
When homeowners hire professionals who are good at their craft, window replacement projects should not be a terrible inconvenience. According to American Window Products Inc., seasoned professionals will be able to complete a replacement window upgrade in a short amount of time depending on the size of the home and the number of windows being replaced.
Replacing windows can be a costly task, but one that will provide a more energy efficient home that can help homeowners save money in the long run.
View post:
How to find the right replacement windows - Journal Times
« old entrysnew entrys »
Page 43«..1020..42434445..5060..»